ENERGY SOLUTION
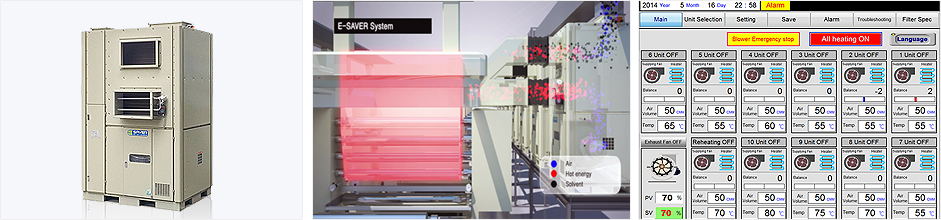
Outstanding Energy Cost Savings Potential
Comparing with the conventional drying facilities prevailing in flexible packaging industries nowadays, E-Saver® provides energy cost savings potential of minimally 60% to 80%, that allows significant cost savings in most of the cases.
Enhancement of Drying Performance
In conventional drying system, with exhaust air recycling adopted for waste heat recovery in particular, vaporized solvent like ink diluent in exhaust air brought back to the drying zone may certainly hamper sufficient drying of substrate. For that reason and/or in order to consistently guarantee sufficiently dried quality all the time, an oversized drying air volume relevant to the excess heat input is adopted by the system operator at his (or her) own discretion, which is normally done by increasing damper opening of the air intake fan, whereas E-Saver® consistently and stably yields adequately dried quality by the iteration function of the built-in control unit of the system.
Computerized User-Friendly Operation
All the parameters for the respective products of diverse flexible packaging printing can be stored and further standardized by data logging. Such data make it possible to carry out optimal setting works anytime, and to immediately start the operation whenever needed, regardless of the product category, utilizing the preset values acquired from the data logged. The operator (or user) is all the time replaceable and shall not necessarily be highly skilled.That is how E-SAVER is accommodating users and how it can be operated by whoever, provided previously trained.
Complete Elimination of Drying Air in Excess
The efficiency of VOC absorption of activated charcoal as a dedusting agent is improved by far, possibly over 70%, as the exhaust air volume and flow speed decreases and the temperature of exhaust is kept around 30 - 35.By incorporating E-SAVER, the installation cost and operational cost extra for the chilling facilities for temperature control of the air and VOC gas mixture being exhausted to fulfill dedusting requirements are entirely avoided.
Technical data
Energy Saving Potential of E-SAVER® for Drying Temperature Variations (on Hourly Basis)
Required Heat is based on the ‘Measured Air Volume’
- Measured Temperature, Intake Air Temperature and Air Volume data are the mean values of real-time measurements from repeated tests
Drying Temp. |
Measured Temp. (℃) |
Intake Air Temp. (℃) |
Measured Air Volume (CMM) |
Intake Air Volume (CMM) |
Specific Weight of Air (kg/m³) |
Required Heat* (kcal) |
Electric Power Require ment* (kWh) |
Electric Power Consumption (kWh) |
Electric Power Saving (kWh) |
Rate of Electric Power Consum ption (%) |
Rate of Electric Power Saving (%) |
---|---|---|---|---|---|---|---|---|---|---|---|
50℃ | 49.0 | 25.9 | 49.7 | 46.1 | 1.2 | 18.263 | 21.2 | 3.0 | 18.2 | 14.1 | 85.9 |
60℃ | 59.2 | 25.9 | 50.4 | 45.3 | 1.2 | 25.811 | 30.0 | 5.6 | 24.4 | 18.7 | 81.3 |
70℃ | 69.2 | 26.2 | 50.4 | 44.0 | 1.2 | 32.727 | 37.8 | 9.2 | 28.6 | 24.4 | 75.6 |
80℃ | 79.0 | 26.2 | 51.8 | 44.0 | 1.2 | 39.813 | 46.3 | 13.2 | 33.1 | 28.5 | 71.5 |
90℃ | 88.8 | 26.2 | 50.5 | 41.7 | 1.2 | 44.727 | 52.0 | 15.6 | 36.4 | 30.0 | 70.0 |
100℃ | 98.7 | 26.2 | 49.4 | 39.8 | 1.2 | 49.386 | 57.4 | 19.8 | 37.6 | 34.5 | 65.5 |
110℃ | 109.6 | 26.5 | 49.6 | 38.8 | 1.2 | 55.144 | 64.1 | 23.6 | 40.5 | 36.8 | 63.2 |
120℃ | 120.2 | 26.9 | 49.7 | 37.9 | 1.2 | 60.506 | 70.4 | 28.8 | 41.6 | 40.9 | 59.1 |
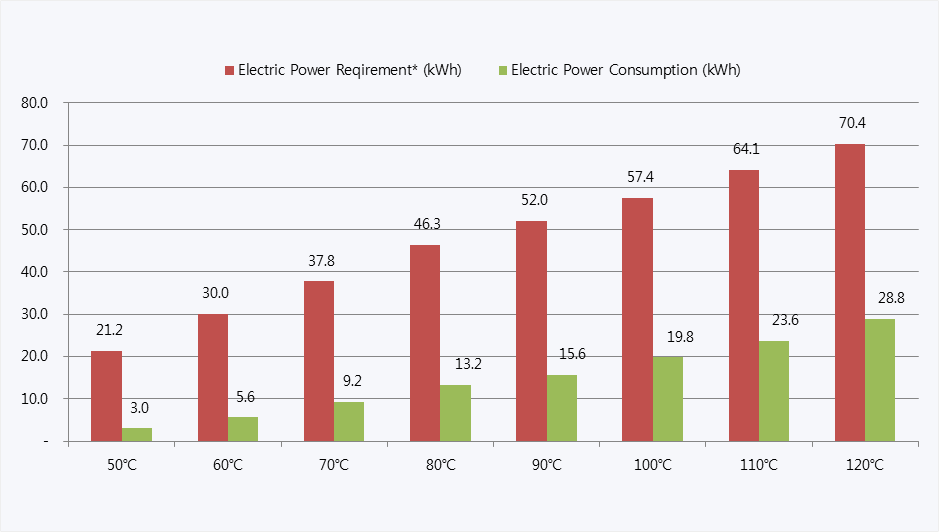