REGENERATIVE THERMAL OXIDIZER (RTO)
A regenerative thermal oxidizer (RTO) converts volatile organic compounds (VOCs) and hazardous air pollutants (HAPs) to carbon dioxide and water vapor through thermal oxidation.RTOs use regenerative heat transfer to achieve very high thermal efficiencies of over 95% percent, which result in very low operating fuel costs — in some cases, zero. That makes them particularly economical for treating low-VOC-concentration process exhaust streams.
Specially, our “New Valve Control RTO system” is only one technology in the world, which can achieve over 99.8% of VOC elimination efficiency continuously in long term. In general, the existing RTO technology is really difficult to maintain its initial VOC elimination efficiency In long terms (even 1~2years) because of its original system design concept & old technology. That’s why many of end-users have been facing another environmental issue against new updated VOC regulation in all countries recently.
Our New Valve Control RTO system is only one solution for these sensitive market requirements.
Benefits
- New Generation RTO Technology “Valve Control System”
(World Technical Patent Registered) - 100% Perfect Seal / “0%” VOCs Leaking
- Extremely easy & simple “One-Touch maintenance” compared with complicated & difficult maintenance of existing Cylinder Rotary or Disk Rotary RTO system.
- Energy Regenerative Efficiency : Upto 97%
- VOCs Concentration Efficiency : Upto 97%
- RTO ⇒ Elimination Efficiency of VOCs : Upto 99.8%
- Extremely Long & Stable VOCs Efficiency Durability
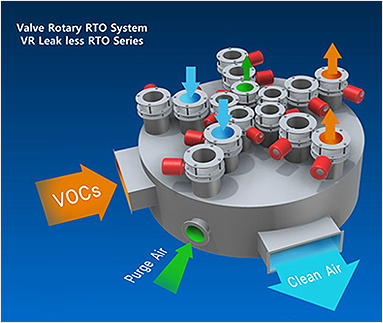
Features
- System ranging from 20cmm to 1200cmm with single assembled modules
- All system can be customized (Design / Space / Structure)
- Basic System Configuration
- RTO Unit only or RTO Unit with Concentrator system
- Perfect Safety Devices & Safety Programming
- Energy Recovery system for Production machines
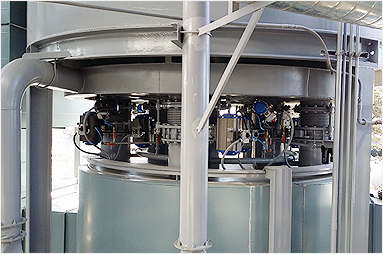
Typical RTO applications include
- Specialty Chemical
- The manufacture of chemicals can generate vent-gas streams and fugitive emissions that must be captured and controlled. BOOSUNG E&C has extensive experience in the design of collection systems, the application of pretreatment particulate removal devices, the oxidation of VOCs, and the treatment of acid gases that sometimes result from oxidation.
- Printing & Packaging
- Gaseous and aerosol particulate emissions come from curing ovens and dryers, from calendaring and fusion operations. BOOSUNG E&C engineers have extensive experience in capturing and treating emissions from extrusion lines; from web offset, rotogravure, flexographic, and intaglio printing processes; and from embossing, lamination, and film production lines — including design for Permanent Total Enclosure.
- Wood Products
- Carbon monoxide, wood dust particulate, condensable organic aerosols, alkali metal containing ash, water-saturated air streams — these are some of the constituents found in VOC exhaust streams emitted from wood products operations. BOOSUNG E&C engineers have treated emissions for many years in plywood, particleboard, oriented strand board (OSB), and wood pellet plants.
- Automotive
- Emissions from impregnation lines, engine casting foundries, engine test facilities, and coating and paint spray booths have been treated by RTOs designed to handle flows up to hundreds of thousands of SCMM per RTO. BOOSUNG E&C engineers have worked on projects in the KOREA, JAPAN, CHINA, TAIWAN and other Asian countries for all major truck and automobile manufacturers for over15 years.
- Pulp & Paper
- Pulp and paper mills present unique and difficult material selection challenges in the application of RTOs and particulate control, as well as in the acid treatment technologies used to control emissions from various process vent streams.
- Pharmaceutical
- Pharmaceutical plant applications include the treatment of various chemical vent streams from mixers and storage tanks, and of exhausts from pill dryers. The latter often contain methylene chloride, which forms hydrochloric acid as a byproduct of oxidation; incorporating wet scrubbers into an RTO application is often an indicated solution.
- Composites & Carbon Fibers
- Products of composite and carbon-fiber manufacturing processes contain resin formulations that emit VOCs upon mixing, heating, and curing. BOOSUNG E&C engineers have designed RTO systems to control these emissions.
- Municipal
- Odors and VOCs from municipal sewage treatment plants can be treated cost-effectively with RTOs.
- Odor Applications
- BOOSUNG E&C engineers have used RTOs to treat malodors from food and animal feed processing plants, rendering plants, sewage treatment plants, and flavorings/odorant manufacture. RTOs are well suited for these applications because of their low operating costs and fuel usage.
- Coating & Painting
- Many coatings and paints still contain VOCs in their formulations. Applied in a liquid state, coating and paint films must be dried, typically in direct-fired ovens and dryers operating at temperatures from 150°F to 600°F. BOOSUNG E&C engineers have designed many high-temperature ducting systems to convey the exhaust streams to RTOs. Various heat recovery systems have also been employed to reduce operating costs for these VOC-rich processes, including waste heat boilers, return-to-process make-up air streams, and building heat with air-to-air heat exchangers. Industries served include coil coating, beverage and food containers, automotive paint shops, medical products, and resilient flooring, among others.